[ad_1]
La spinta incessante del settore dei semiconduttori a fornire costantemente prestazioni ed efficienza energetica migliori ha tradizionalmente portato a geometrie dei dispositivi sempre più piccole. Tuttavia, queste dimensioni ridotte stanno iniziando a incidere sulla complessità del processo e stanno diventando eccessivamente costose da produrre. Nessuno può negare che stare al passo con la Legge di Moore sia sempre stata una sfida, ma forse potrebbe essere il momento di una discussione seria.
L’approccio alternativo qui presentato implica una transizione generale verso metodi di packaging avanzati e strutture 3D, dove l’obiettivo di continuare a migliorare la velocità, la portata della capacità di calcolo e l’efficienza energetica dei nuovi prodotti a semiconduttori che supportano le applicazioni di intelligenza artificiale può essere raggiunto senza solo ridurre le risorse di base. geometria del dispositivo a semiconduttore.
Infatti, i metodi di confezionamento avanzati offrono nuove strategie di integrazione che combinano le tecnologie a livello modulare, attraverso la tecnologia di interconnessione chip-to-chip che consente la combinazione di processi di piccole dimensioni ad alto rendimento, in sistemi multi-chip integrati più grandi e complessi, senza tecnologia avanzata a livello di gate del nodo per grandi dimensioni a stampo singolo che sono più difficili da produrre. Tuttavia, anche se la geometria del singolo dispositivo può allentarsi, questi nuovi approcci pongono tuttavia elevate esigenze di precisione e allineamento sempre maggiori per realizzare la progettazione del sistema integrato e il necessario controllo del processo di produzione.
Ciò, ovviamente, richiede che le tecnologie di controllo del movimento tengano il passo con questi requisiti di velocità, accuratezza e precisione combinate senza precedenti (Figura 1). Allo stesso tempo, nessuno vuole vedere diminuire i parametri di produttività, il che crea una spinta costante verso una maggiore accuratezza e precisione a un rendimento di produzione elevato.
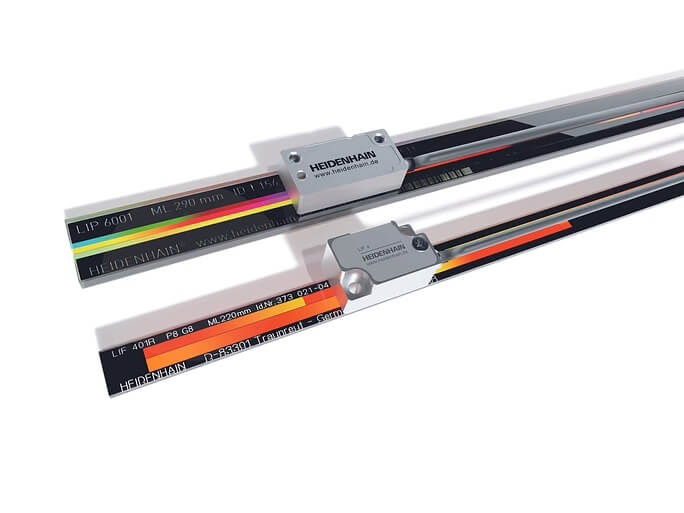
Richieste di maggiore precisione
Un esempio di un processo di produzione relativamente nuovo è il collegamento ibrido die-wafer, in cui i die sono impilati uno sopra l’altro e interconnessi tramite sottili interconnessioni in rame. Ciò consente una densità di connessioni precedentemente irraggiungibile, superando i limiti delle tradizionali tecnologie bump in rame e riducendo notevolmente il ritardo e l’attenuazione del segnale.
Tuttavia, una densità maggiore porta a tolleranze più strette e quindi è necessario un controllo del movimento molto più accurato nel processo di incollaggio rispetto alle alternative convenzionali.
Un altro nuovo sviluppo in questo segmento è il fan-out wafer-level packaging (FOWLP), che include nuovi substrati più stabili. Nonostante sia stato inventato più di 20 anni fa, il design del pacchetto fan-out ha raccolto un notevole interesse nel mercato odierno ed è attualmente visto come una valida alternativa al fan-in, in particolare negli ultimi cinque-dieci anni.
Rispetto ai package standard a livello di wafer, FOWLP consente specifiche di input/output impressionanti con un ingombro più compatto, offrendo allo stesso tempo prestazioni termiche ed elettriche superiori. Man mano che il die diventa gradualmente più piccolo, il packaging fan-out consente le densità di interconnessione molto elevate presenti sui die più piccoli.
Sfortunatamente, il processo di produzione richiesto è piuttosto complesso. FOWLP richiede la ricostituzione del wafer con un die incorporato in materiali a basso costo, che consentono al silicio ad alto costo di diventare più efficiente. Tuttavia, questo processo è abbinato a fasi di fabbricazione precise, che rallentano la produzione, mettendo a dura prova i costi di proprietà (CoO) dei produttori. La relazione è chiara: maggiore è la densità, più fine è il passo di connessione e maggiori sono i requisiti di velocità e precisione di posizionamento.
Bilanciamento di precisione e produttività
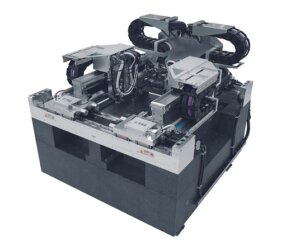
La scelta degli strumenti nel settore dei semiconduttori è guidata prevalentemente dal CoO. Per le applicazioni back-end, il CoO è generalmente definito come una combinazione di costo per obbligazione e rendimento. Entrambi i parametri sono direttamente collegati alla precisione di posizionamento e alla produttività del sistema di movimento utilizzato nel processo di integrazione dei chip (Figura 2). Non esiste tolleranza per la perdita di rendimento dei circuiti integrati finiti, pertanto l’affidabilità del processo di integrazione del packaging deve essere estremamente elevata.
Si può avere tutta la larghezza di banda, l’intelligenza artificiale e l’ottica del mondo, ma niente di tutto ciò ha importanza quando uno strumento per semiconduttori non può raggiungere una precisione a livello nanometrico senza compromettere la produttività. Quando l’obiettivo è effettuare misurazioni ad alta precisione il più rapidamente possibile, la velocità massima dell’asse di un sistema di movimento deve essere raggiunta con un tempo di assestamento minimo o una misurazione al volo. Di solito sono presenti molteplici compromessi e quindi, in base alla progettazione, le architetture dei sistemi di movimento convenzionali sono ottimizzate per un’elevata precisione di posizionamento o per un’elevata produttività.
Per ottenere l’ambita combinazione di velocità, precisione e stabilità sono necessari processi e tecnologie di movimento più avanzati, ovvero encoder per acquisire posizione e velocità, nonché sistemi di controllo del movimento per il movimento ad alta precisione di strumenti e componenti.
I sistemi di Motion Control sono destinati ad assumere un ruolo di primo piano
Progressi come FOWLP introducono molteplici variabili nel processo di produzione, creando una maggiore probabilità di imperfezioni nel prodotto finale. Inoltre, questo approccio richiede anche estrema velocità e precisione millimetrica costante per una produzione di semiconduttori efficiente e redditizia.
Due sono le tecnologie fondamentali che si stanno rivelando decisive per raggiungere il successo con questa nuova strategia produttiva. Il primo elemento chiave di questo approccio è l’encoder HEIDENHAIN LIP 6000 molto compatto che offre un’impressionante stabilità del segnale di 0,4 nanometri a 1 MHz, consentendo al sistema di movimento di raggiungere tempi di ricerca e stabilizzazione di millisecondi. In secondo luogo, i controlli ETEL utilizzano algoritmi per calcolare le prestazioni ottimali del percorso per l’ispezione simili a quelli utilizzati per aiutare i conducenti di auto da corsa a seguire la traiettoria di gara più ottimale.
Il sistema di movimento TELICA di ETEL è una piattaforma avanzata di sistemi di movimento altamente dinamici dedicata ai processi di semiconduttori backend di precisione che consente al processo di raggiungere la precisione di posizionamento inferiore al micron richiesta per i pacchetti avanzati di prossima generazione. Questo elevato livello di precisione viene mantenuto su un’area di lavoro fino a (870 x 800 mm), che consente contemporaneamente cicli di lavoro e produttività molto elevati.
TELICA sta ora introducendo un approccio completamente nuovo che comprende un circuito metrologico secondario a livello del piano di processo. Ciò riduce drasticamente gli errori di Abbé e la relativa mancata corrispondenza del posizionamento tra lo strumento di processo e il substrato. Gli encoder multidimensionali garantiscono che il livello di precisione del posizionamento venga raggiunto fino a sei gradi di libertà, mentre i motori “iron core” raffreddati ad acqua consentono cicli di lavoro estremi ma affidabili.
Il concetto del telaio metrologico riduce inoltre qualsiasi circuito di feedback delle vibrazioni all’interno del sistema che agisce sulla punta dell’utensile, riducendo così al minimo i disturbi nelle fasi di posizionamento, processo o ispezione desiderate. Man mano che emergono capacità di posizionamento di target ad alto rendimento nell’ambito inferiore a 50 nm per strategie di integrazione di chiplet eterogenei, soprattutto se si considerano i futuri processi di bonding ibrido, un sistema di movimento completamente integrato che includa una piattaforma di isolamento attivo, uno stadio multiasse, un’elettronica avanzata di controllo del movimento, e l’architettura dell’algoritmo diventa necessaria.
Conclusione
L’incessante spinta dell’industria dei semiconduttori verso le strutture 3D e le emergenti tecniche di packaging avanzate per raggiungere gli obiettivi “Più della legge di Moore” richiedono processi di produzione sempre più complessi, precisi e affidabili.
Questi nuovi sviluppi nel campo del controllo del movimento stanno consentendo ai produttori di soddisfare e superare questi severi requisiti di precisione, pur mantenendo una produttività e costi di proprietà più che soddisfacenti. L’industria dei semiconduttori continuerà a innovare oltre gli apparenti limiti fisici della produzione di transistor al silicio e a produrre dispositivi a livello di sistema che offrano prestazioni superiori abbinate a efficienza energetica, il tutto all’interno di un ingombro di package standard o magari estendendo le dimensioni del package dei moduli.
La dissipazione di potenza e calore da questi complessi sistemi multi-chip continuerà a rappresentare una sfida per il settore poiché la domanda di elaborazione continua a crescere nelle applicazioni IA ad alta velocità.
Questo articolo è apparso per la prima volta nell’Annuario 3D InCites 2024. Leggi la questione qui.
[ad_2]
Source link